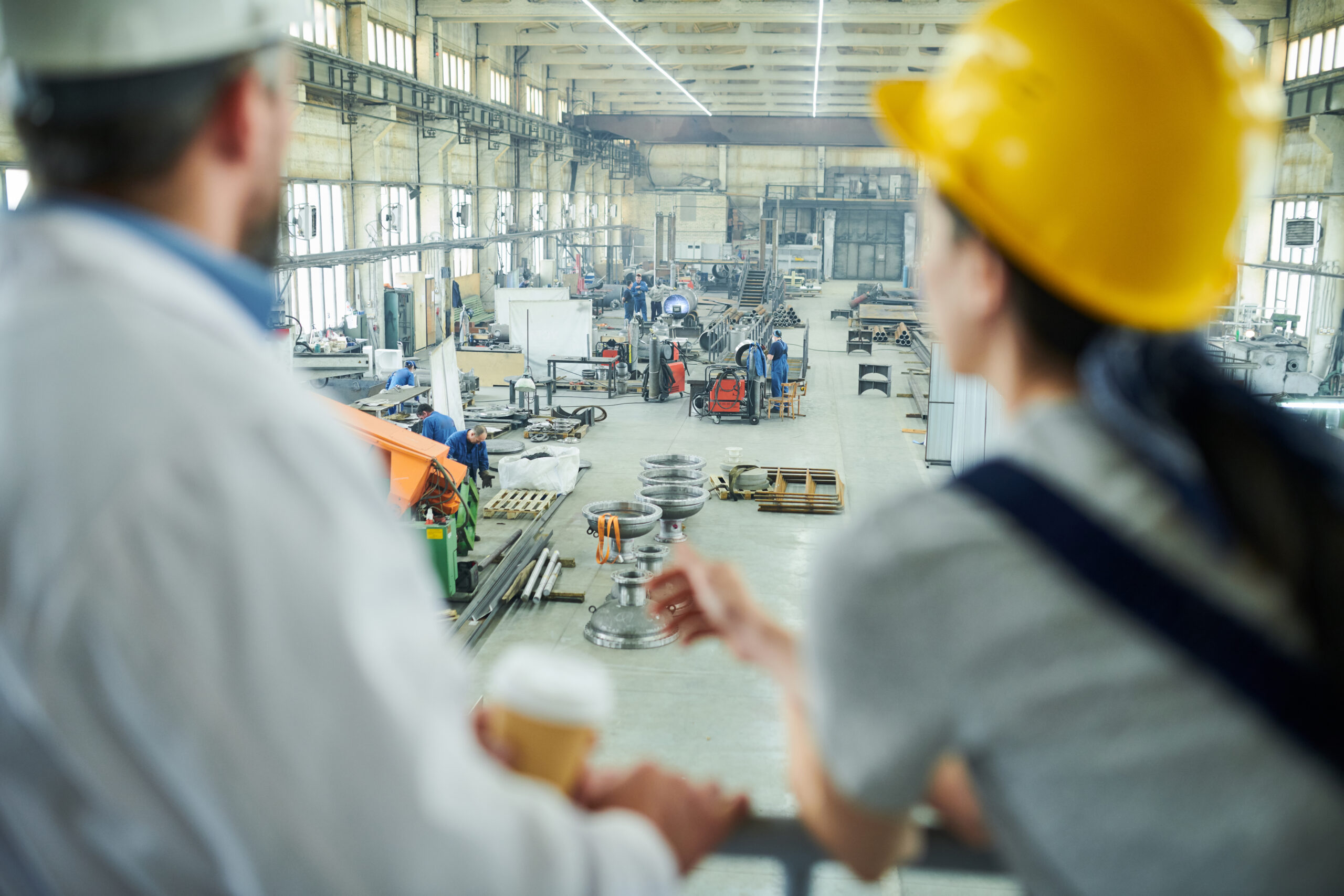
05 Oct Scaled Solutions Group’s Best Practices for Production Orders and Secondary Processing in Epicor Prophet 21 P21
As seasoned experts with over 20 years of experience implementing Epicor Prophet 21 across various industries, Scaled Solutions Group has developed a comprehensive approach to managing production orders and secondary processing. We ensure our clients maximize the benefits of P21 by following a structured methodology designed to optimize workflows, enhance inventory management, and streamline complex production processes. Here, we outline our detailed best practices for using production orders and secondary processing within Epicor P21.
1. Creating a Production Order in P21
The creation of a production order begins with Assembly Maintenance in P21 (found under Orders > Production > Order Maintenance). A key prerequisite is to ensure that the assembly item is already set up in the system through Item Maintenance.
Our recommended best practices for configuring production orders include:
Pricing Options
- By Assembly: Ideal when selling the whole assembly as a single item with a fixed price. Most of our clients prefer this option for its simplicity.
- By Assembly Using Components: Useful when pricing based on individual component costs, rolling up to the total assembly price.
- By Components: Suitable when the pricing needs to be detailed at the component level, allowing for granular control.
Best Practice: Choose the pricing strategy that aligns with your business model and customer requirements. Most distributors find that using the “By Assembly” option provides a straightforward and customer-friendly pricing approach.
Disposition Settings
- Default to Back Order to allow assemblies to be back-ordered when not in stock.
- Use Special Order for items not typically stocked and that require vendor orders.
- Set to Cancel for items that will not be stocked.
Best Practice: For most clients, leaving the disposition setting at “Back Order” ensures a seamless replenishment process while minimizing disruptions in order fulfillment.
Usage Tracking
- Enable usage tracking either at the assembly level, the component level, or both. Tracking usage is crucial for optimizing inventory management and accurate demand forecasting.
Best Practice: For comprehensive data analysis and improved planning, we recommend capturing usage at both the assembly and component levels.
Disassembly Option
- Use the disassembly feature to return individual components to stock if the assembly needs to be broken down.
Best Practice: Activate this feature when your production processes involve recycling or repurposing components from completed assemblies.
Production Order Processing
- Enable production order processing to generate production orders for assemblies, providing greater control and traceability through each production phase.
Best Practice: Utilize production order processing for assemblies requiring multiple steps or quality checks. If the assembly is simpler and only requires picking and shipping, consider using the “kit” option.
2. Adding Components to an Assembly
After defining the assembly properties, add the necessary components:
- Navigate to the Component section within Assembly Maintenance.
- Select pre-defined items and specify the required quantity for each assembly.
- Save the assembly once all components are added.
Best Practice: Set accurate quantities for each component to maintain inventory levels and avoid over- or under-production. Proper setup here ensures smooth allocation during production order processing.
3. Creating a Sales Order and Auto-Generating a Production Order
With the assembly created, proceed to sales order creation:
- Enter customer details and select the assembly item.
- If the item is not in stock, the disposition will automatically change to “P for Production.”
- Input pricing details, save the sales order, and allow P21 to auto-generate the production order.
Best Practice: Enable automatic production order generation in transaction windows to streamline order processing and minimize manual intervention.
4. Generating Production Orders Using Purchase Order Requirements Generation (PORG)
For a more dynamic approach to creating production orders, use the PORG tool:
- Navigate to PORG in P21, entering relevant details such as buyer, location, and items.
- After requirements generation, decide whether to Produce or Purchase the items.
- Create production orders as needed.
Best Practice: Regularly use PORG for a batch approach to managing production requirements, ensuring timely production and stock replenishment based on current demand.
5. Manual Creation of Production Orders
When necessary, production orders can be created manually:
- Go to Production Order Entry, input details like company, location, and item.
- Manually assign the production order to an existing sales order.
Best Practice: Utilize manual entry for custom or special production runs that require specific handling outside of the standard automated workflows.
6. Processing a Production Order
- Verify required components using the Components tab.
- Allocate inventory for components, print the production order form, and generate pick tickets.
- Automated Scheduling: Schedule pick ticket printing to optimize order processing efficiency.
Best Practice: Implement automated pick ticket printing to streamline production order processing and reduce manual tasks for warehouse staff.
7. Secondary Processing Overview
Secondary processing is crucial for managing additional steps like quality checks or external processing. Here’s how to manage it efficiently:
Setting Up Predefined Routing
- Create routing under Orders > Secondary Processing > Maintenance > Predefined Routing.
- Define the Route Name, Raw and Finished Items, yield ratio, and required process steps.
Best Practice: Set up predefined routings for recurring secondary processes to maintain consistency and reduce setup time for each production run.
Running a Secondary Process
- Enter a sales order for the item.
- Allocate raw items and start production, moving through predefined routing steps as needed.
Best Practice: Maintain accurate tracking of each step in the secondary process to identify bottlenecks and improve production flow.
Generating a Purchase Order for External Processing
- If a step requires external processing, generate a purchase order using the Generate Consolidated Process POs tool.
- Enter the process number and create the purchase order.
Best Practice: Automate purchase order generation for external processes to ensure timely procurement and avoid delays in production.
Completing Secondary Processing
- Complete the purchase order receipt upon receiving processed items back.
- Move the items through the final quality check and allocate to the sales order.
Best Practice: Conduct a final quality check before allocating the item to the sales order to ensure that only items meeting quality standards reach customers.
8. Handling Complex Assemblies and Sub-Assemblies
Epicor P21 allows for the creation of assemblies containing multiple sub-assemblies. The system automatically generates production orders for each sub-assembly, ensuring a structured workflow where sub-assemblies are completed and then allocated to the main assembly.
Best Practice: Use sub-assembly production orders to manage complex assemblies effectively, ensuring each component is built and tracked systematically.
Final Thoughts
Adopting these best practices in managing production orders and secondary processing within Epicor P21 can significantly enhance manufacturing and inventory management. By leveraging automated order creation, predefined routing, and integrated secondary processing, businesses can optimize production workflows, maintain accurate inventory levels, and fulfill orders efficiently.
For further guidance or support on implementing these best practices in your P21 environment, Scaled Solutions Group is here to help. Feel free to reach out to us for expert advice tailored to your specific operational needs. Scaled Solutions Group offers a comprehensive range of ERP p21 Implementation consulting services designed to help businesses achieve seamless ERP implementations and optimize their operations. For more information, contact Scaled Solutions Group at (866) 957-8419 or info@scaledsolutionsgroup.com or visit www.Get-Scaled.com.