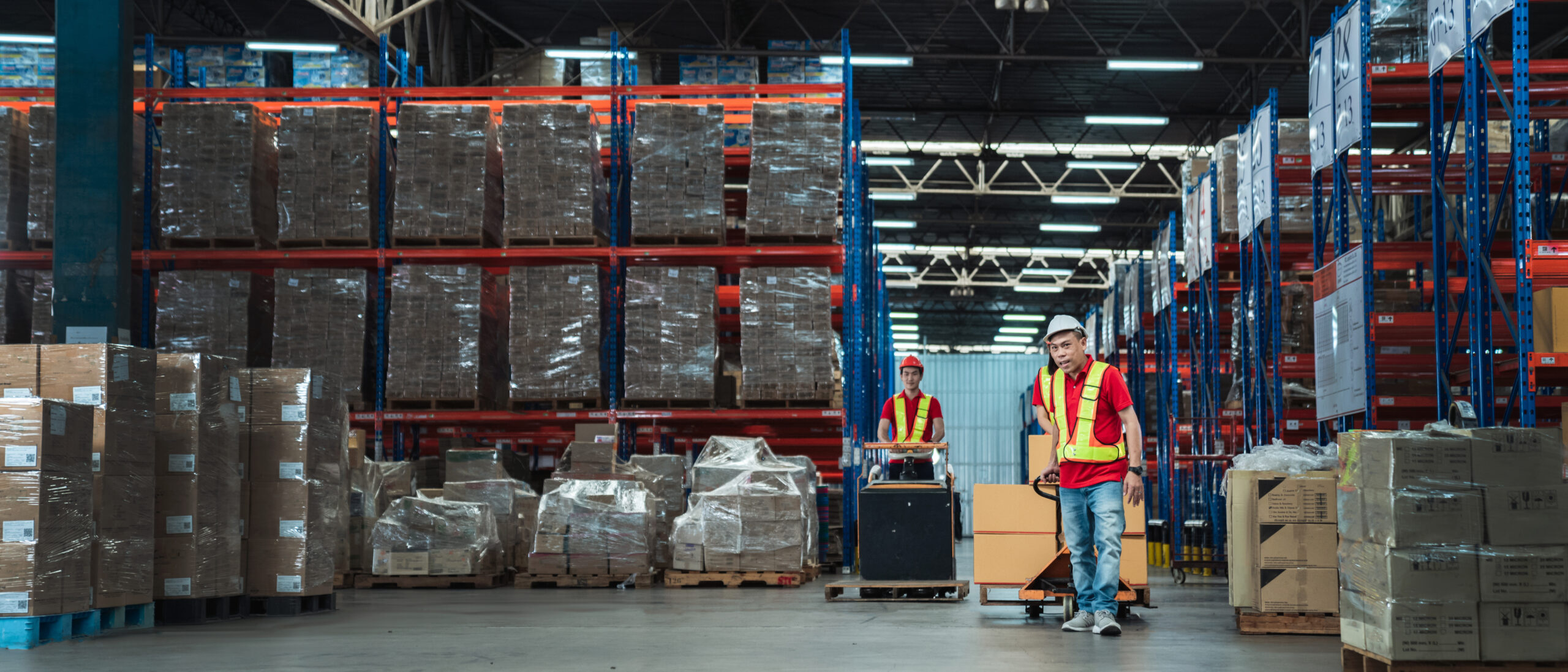
21 Oct Scaled Solutions Group: Best Practices for Stock Adjustments in Epicor Prophet 21 P21
At Scaled Solutions Group, we understand that accurate inventory adjustments are essential for maintaining efficient operations and data integrity. Our expert P21 Implementation team offers comprehensive guidance to ensure your stock adjustments within Epicor Prophet 21 (P21) are managed smoothly and effectively. Below are the step-by-step processes and best practices we employ to help your organization handle lot and stock quantities, as well as create and modify reason codes for adjustments. Mandatory steps are marked with a *.
1. Adjusting Lot Quantities for an Item
Managing lot quantities accurately is critical, especially when your operations rely on precise tracking. Our approach ensures each adjustment is handled with precision to maintain data integrity.
Steps:
- *Access the Inventory Module: Open the Inventory module in Epicor Prophet 21.
- *Select Lot Adjustment: Navigate to the Transaction menu and choose “Lot Adjustment.”
- *Enter General Information: On the General tab, input the Company ID, Location ID, and Item ID. The system will display existing lot information on the Lots tab.
Tip: The system restricts selection to items configured to track lots. - *Adjust Quantities on the Lots Tab: Modify the “New Quantity On Hand” for each lot as needed. Ensure that the new quantity is greater than or equal to the “Quantity Allocated” to avoid errors.
- Update the Unit of Measure (UOM): If changing the item’s UOM, adjust the “New Quantity On Hand” to reflect the new unit accurately.
- Add a New Lot (Optional): Define a new row and assign a new lot if required.
- *Save the Changes: Click Save to confirm the adjustments.
Tip: Ensure that the “Total New Quantity On Hand” equals the current Quantity On Hand, and that all stock is assigned to specific lots before saving.
Best Practices:
- Verify Quantity Allocated values to prevent adjustment errors.
- Double-check UOM changes to ensure accurate tracking and reporting.
- Document adjustments to create a clear audit trail and support transparency.
2. Adjusting Stock Quantities
Adjusting stock quantities effectively can address discrepancies, manage damages, and support restocking efforts. Our experts ensure these adjustments are handled efficiently to maintain accurate records.
Steps:
- *Open the Inventory Module: Access the Inventory module.
- *Select Inventory Adjustments: Choose “Inventory Adjustments” from the Transaction menu.
- *Enter Adjustment Details: On the Adjustments tab, specify the Company ID and Location ID where the adjustment will occur.
- *Provide Adjustment Reason, Period, and Year: Enter a reason for the adjustment, and select the appropriate financial period and year for posting.
- *Select the Item: In the Items tab, enter the Item ID. The system will show the Description, Quantity On Hand, and Quantity Allocated.
- *Input the Adjustment Amount: Specify the quantity to add or subtract in the “Adjustment Amount” field. The system will automatically display the “New Quantity On Hand.”
Tip: Use positive values to increase stock and negative values to decrease stock. - Modify the Unit of Measure (UOM) if Necessary: Adjust the default UOM to match the actual units being added or removed.
- Enter Unit Cost: Provide the unit cost for the items being adjusted.
- Approval Process (If Enabled): If “Use Approvals” is active, adjustments must be approved before they become permanent. Once approved, changes cannot be modified or deleted.
- *Save the Adjustment: Click Save to apply the stock adjustment.
Best Practices:
- Double-check adjustment reasons, periods, and UOM to ensure accuracy.
- Utilize approval workflows to add a layer of validation, especially for high-value adjustments.
- Maintain a detailed log of adjustments for internal reviews and audits.
3. Editing an Existing Reason Code for Stock Adjustments
From time to time, it is necessary to update existing reason codes to reflect new business conditions or clarify their usage. We help your team make these adjustments seamlessly.
Steps:
- *Open the Inventory Module: Navigate to the system’s Inventory module.
- *Access Adjustment Reason Maintenance: From the System menu, select “Adjustment Reason Maintenance.”
- *Enter the Reason ID: Locate and enter the ID of the reason code you wish to modify.
- Modify Details as Needed: Update the Reason description or the associated GL Account Number.
- *Save the Changes: Click Save to finalize the modifications.
Best Practices:
- Regularly review and update reason codes to align with evolving business practices.
- Ensure reason descriptions are clear and specific to avoid confusion during audits.
4. Creating a New Reason Code for Stock Adjustments
If new situations arise that require unique tracking, creating new reason codes ensures accurate documentation of adjustments. Our team can help set these up effectively.
Steps:
- *Open the Inventory Module: Begin by accessing the Inventory module.
- *Select Adjustment Reason Maintenance: Choose “Adjustment Reason Maintenance” from the System menu.
- *Enter a New Reason: Provide a clear, specific reason for the adjustment (e.g., “Goods damaged in transit”).
- Assign the GL Account: Input the GL account number associated with this reason, ensuring correct posting in financial records.
- *Save the New Reason: Click Save to create the new reason code.
Best Practices:
- Develop specific and standardized reason codes across departments.
- Ensure appropriate GL accounts are assigned to facilitate accurate accounting.
Why Choose Scaled Solutions Group?
With over 20 years of experience, Scaled Solutions Group specializes in implementing and optimizing Epicor Prophet 21 P21. Our team of certified Epicor P21 implementation professionals ensure that your inventory adjustments are consistent, reliable, and aligned with your operational needs. We prioritize data accuracy, transparency, and streamlined processes, helping your business achieve enhanced inventory management and financial reporting. Contact us to learn how our expertise can make a difference in your inventory management practices. Scaled Solutions Group is here to help. Feel free to reach out to us for expert advice tailored to your specific operational needs. Scaled Solutions Group offers a comprehensive range of ERP p21 Implementation consulting services designed to help businesses achieve seamless ERP implementations and optimize their operations. For more information, contact Scaled Solutions Group at (866) 957-8419 or info@scaledsolutionsgroup.com or visit www.Get-Scaled.com.